Partners
TERMIS
Click here to view the memorandum of understanding for ISBF and TERMIS.
Sponsors
Aspect Biosystems
Aspect Biosystems is a bold team of innovators & entrepreneurs from all over the globe. Bringing together different backgrounds, perspectives, and expertise defines who we are and what we do.
We believe that diversity drives disruptive ideas that will transform our health.
We are passionate about collaborating with researchers and industry around the world to push the limits of our technology and make a real impact.
We’ve combined the power of microfluidics and 3D bioprinting to fuel medical research and the development of bioprinted therapeutics that will save lives and make people healthier.
CollPlant Ltd.
CollPlant (NASDAQ:CLGN) is a regenerative medicine company focused on developing and commercializing BioInks for 3D bioprinting and tissue repair products. CollPlant’s products are based on its recombinant human collagen (rhCollagen) which is produced in genetically engineered tobacco plants using CollPlant’s proprietary technology. The Company’s products, which address 3D bioprinting, medical aesthetics, orthopedics and advanced wound care, are ushering in a new era in regenerative medicine. Commercialization of CollPlant’s products was initiated in 2017. They address multi-billion dollar markets worldwide.
Learn More about CollPlant
Vision
Be the leaders in regenerative medicine, helping people live longer and better through our innovative collagen technology.
Technology
CollPlant’s technology is the only commercially viable technology currently available to produce true Type I human collagen. Collagen is an essential building block of the human body, providing structural support and biological signals to connective tissues and organs, and therefore it is a crucial component for tissue regeneration. CollPlant’s proprietary technology includes the introduction into tobacco plants, of 5 human genes that are essential for the synthesis of Type I collagen. The tobacco plant then proceeds to yield human collagen that is superior to the collagen(s) currently in the market, sourced from animals, or even human cadavers. rhCollagen is identical to natural human collagen, therefore it does not elicit an immune response in humans. Its plant origin yields a safe product with more consistent properties, making it the ideal building block/scaffolding molecule for regenerative medicine. CollPlant’s rhCollagen is a broadly applicable technology platform that is cost effective and enables products for medical uses with superior biological and physical properties.
Products
- BioInks for 3D Bioprinting of Tissues and Organs: Recently, 3D bioprinting has been gaining momentum in many medicinal applications to address the need for complex scaffolds needed for generation of tissues and organs suitable for transplantation. CollPlant’s rhCollagen-based BioInks are ideal for 3D bioprinting due to their safety profile, as well as their biological and physical properties. rhCollagen enables an unlimited, economical supply of organs around the world. Currently, 3D bioprinting is primarily used in R&D, as the technology is moving towards commercialization of manufactured lifesaving organs including lungs, liver, kidney and heart. The ability to manufacture organs could save nearly a million lives in the U.S. alone, where 30,000 organ transplants are done each year and 900,000 people die every year due to organ impairment.
ROKIT Healthcare
“Aging is a Disease” and “Nature is Prescription”
ROKIT Healthcare strives to resolve the global aging problem through organ regeneration and compression of morbidity. We make every effort for a better quality of life for the humanity.
ROKIT Healthcare is a global healthcare company committed to providing the safest and most effective autologous organ regeneration platform using its proprietary biofabrication technologies across all types of applicable diseases in the field of regenerative medicine.
Learn More about ROKIT
Through a convergence of know-how’s and innovation in the areas of R&D (i.e. 3D bioprinting, autologous stem cell technologies, and human-derived biomaterials), surgical medicine, and regulatory affairs, ROKIT Healthcare believes in supplying customized organ regeneration platform services that will drastically change the way we trust and manage the health of our own body.
History:
ROKIT was founded in 2012 by Seok Hwan You as a 3D printing technology company. From 2013 to 2015, the company released several desktop 3D printer lines for applications in educational training, fashion, design, food and industrial manufacturing.
In April 2016, the company entered the biomedical industry with the launch of INVIVO, a cell and biomaterial 3D printer equipped with clean chamber technology. It is one of the first commercialized desktop bioprinters made in Korea.
In addition to being a printer manufacturer, ROKIT works as a medical contractor that partners with state agencies, biotechs and academic research centers to develop applications of the 3D bioprinting technology in the hospital operating room.
In October 2016, ROKIT was awarded a $3 million grant by the South Korean government to co-develop an in-situ 3D bioprinting system for skin regeneration. In Dec 2017, ROKIT announced the establishment of a European R&D center in Germany as a research collaborator with Fraunhofer IBMT. In 2018, ROKIT signed agreements with plastic surgery clinic GNG in Korea to develop processes and technology to create 3D printing-guided regeneration of skin and cartilage tissues for use in nose and ear reconstruction. In 2019, ROKIT Healthcare has won $30 million worth of investment, and is striving toward the development and launching of new therapies in regenerative medicine.
Mission & Vision:
ROKIT envisions to change the world by serving patients through personalized regenerative therapies with our customized artificial organ platforms.
- Technologies to be highlighted:
Therapeutics:
ROKIT is developing platform services in the areas of Dermatology, Orthopedics, Cardiology, and Ophthalmology (skin regeneration, cartilage regeneration, heart patch regeneration, retina regeneration, and hair regeneration.) ROKIT will provide organ regeneration platforms that combine a device, materials, and surgical protocols in a ready-to-use package in the operating room.
Life Sciences:
For the R&D sector, ROKIT Healthcare offers technologies in 3D biofabrication and biomaterial development using the cell sheet technology.
ROKIT Healthcare offers INVIVO, a polymer and hydrogel extrusion 3D printer equipped with built-in sterilization systems, which allows researchers to fabricate soft and hard 3D biological structures with cells.
ROKIT Healthcare also offers whole extracellular matrix (ECM)-based bioink supplements, developed using the cell sheet technology. The technology employs cells on a polymer bed of tunable stiffness mimicking anywhere from soft to hard microenvironments. This allows the production of human cell-derived ECM with the native architecture of the matrix retained and customizable to various tissues.
- Product:
INVIVO: Made by Nature. Healthcare Innovation by INVIVO.
INVIVO was developed for biomedical researchers and material engineers to pattern cells, biomolecules, and polymers to explore multi-material 3D composite structures, from tissues to novel biocompatible materials.
INVIVO provides three types of printing technologies with a comprehensive temperature control from -5 to 350C:
- Syringe dispenser (and print bed): -5 to 80C
- Filament extruder: RT to 250C
- Hot-melt pneumatic dispenser: RT to 350
INVIVO’s unique features include
- UV / LED curing: 365/395/405/450/460nm, automatic on/off
- LED light on/off (to enable a pitch black chamber for photo-sensitive materials)
- 48, 96-well, microscope slide chamber, 35mm dish printing
- Able to adjust Z-leveling and load/unloading while printing is in progress
- Customizable syringe volume: 10mL (default), 3mL / 1mL
- INVIVO-specific slicing software with 40+ process parameters open to the user for maximum flexibility in print quality control
Contacts:
Name: Heon Ju Lee, Ph.D
Position: Managing Director
Email: hlee@rokit.co.kr
Phone Number: +82 2 867 0182
Secondary contact:
Name: Sean Seonwoo, MS
Position: Project Manager
Email: seonwooh@rokit.co.kr
Phone Number: +82 10 8682 2811
Rousselot® Biomedical
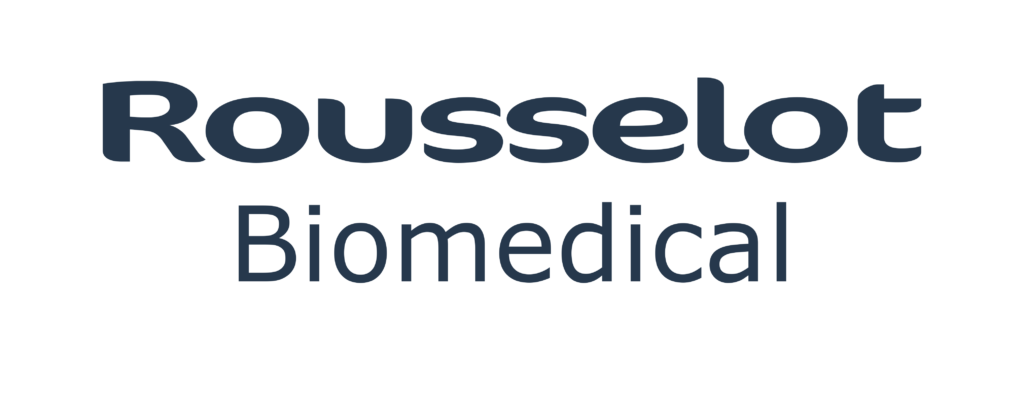
As the most recent strategic segment within Rousselot®, we have drawn upon Rousselot’s 125+ years of worldwide expertise and proven track record of pharmaceutical gelatins and collagens to develop X-Pure®, an innovative range of purified gelatins and collagens specifically designed for (bio)medical applications. Offering unique advantages to assure performance, quality and safety, X-Pure is backed by strong scientific data and on-going research. Rousselot Biomedical is committed to facilitating the use of X-Pure in your applications and to help “Advancing medical science”.
Learn More about Rousselot Biomedical
Rousselot® Biomedical develops highly purified, modified and non-modified gelatins customized for reliable and scalable products. Pharmaceutical grade X-Pure® non-gelling, gelling and its modified versions, such as X-Pure® GelMA or X-Pure® GelDAT, are ideal for 3D printing, tissue engineering, regenerative medicine, vaccines, drug delivery systems, cell therapies, surgical and parenteral applications, wound healing and organ on a chip.
Products
X-Pure® gelatins:
Low endotoxin (<10 EU/g) natural biomaterial derived from denatured collagen, a component of the extracellular matrix;
Promotes cell adhesion and proliferation;
Biocompatible and biodegradable;
Batch to batch consistency;
Reliability and security of supply;
Full and validated traceability of raw materials upon request.
X-pure gelatins can be further chemically functionalized to our customers’ specific needs by customizing the products average molecular weight and the type and degree of chemical modification.
Our X-Pure modified gelatin portfolio is a good example of Rousselot’s Biomedical co-development approach. By listening to our customers’ needs for a low endotoxin GelMA with consistent mechanical properties, X-Pure® GelMA became a tailor-made ingredient for high-end biomedical applications currently challenged in the pre-clinical phase of human clinical trials. More recently, the launch of X-Pure® GelDAT, has met the market demand for a purified and highly adhesive modified gelatin.
X-Pure® GelMA:
Photo-polymerizable X-Pure® gelatin with customized Degree of Modification and Molecular Weight for tunable physical properties.
Rousselot’s controlled production allows the development and manufacture of customized highly purified gelatin-based biomaterials specific for your unique application.
X- Pure® GelDAT:
The world’s first purified Gelatin Desaminotyrosine. Developed to overcome the challenges researchers face when using gelatin tyramine (GelTYR).
Cross-linked by both enzymatic reaction or photo-induction and customized Degree of Modification and Molecular Weight for tunable physical properties.
Applications of X-Pure®, X-Pure® GelMA, and X-Pure® GelDAT: Hydrogels, particles and films for 3D printing, tissue engineering, regenerative medicine, vaccines, drug delivery systems, cell therapies, surgical and parenteral applications, wound healing and organ-on-a chip.
Contact:
Mr. Jeff Daelman
jeff.daelman@rousselot.com
T&R Biofab Co. Ltd.
T&R Biofab is a tissue engineering company which has experienced a rapid growth with our 3D bioprinting platform technology. We aim to claim the title for the best biomedical engineering company in the world that is capable of printing human organs and tissues in vitro for clinical transplantation. We strive to cure the world of life’s pain and realize its value through our research.
Learn More about T&R Biofab
Core Technology
We develop and manufacture bioresorbable scaffolds, organoids, and 3D cell therapy based on our unique 3D bioprinting platform technology, such as decellularized ECM-derived bioinks and 3D bioprinters.
3D Bioprinter
-
-
- T&R Biofab’s 3D printer(3DXPrinter) allows for printing of various materials, including biodegradable polymers, ceramics and cell-laden bioink. Our printers are well suited for the printing of medical devices for transplantation, tissue regeneration, hydrogels, and organoid models.
-
Bioink (deCelluid™-skin, bone, cartilage)
-
-
- Made from porcine decellularized extracellular matrix (dECM), deCelluid™ is used to provide a favorable environment for cells (especially stem cells) to grow in conditions which are biomimetic containing the natural bioactive molecules found in native tissue.
-
Applications
Bioresorbable Scaffold
-
-
- A bioresorbable scaffold is a medical device for assisting reconstruction and regeneration of defective or damaged tissue. Our 3D printed scaffolds feature the use of a porous structure made from biocompatible polymers, which allows for the infiltration of native tissues into the implant which naturally degrades over time.
-
Organoid
-
-
- We are developing 3D printed organoids which can solve ethical and scientific problems associated with animals testing. Artificial models of human organs and tissues made through a mixed approach of 3D printing and stem cell culturing techniques. Organoids are a product which can be used as an alternative to animal testing or as a drug screening system for novel pharmaceuticals. (currently under development)
-
3D Cell Therapy
-
-
- We are also developing 3D printed cell therapeutic devices such as a pre-vascularized cardiac patch and artificial blood vessels. 3D printed cell patch or artificial tissue can enhance the therapeutic efficacy for various diseases. The spatial patterning of multiple cells can improve cell-to-cell interactions and promotes increased functionality of the printed cells. (currently under development)
-
Products
-
-
- 3DXPrinter (3D Bioprinter), deCelluid™-skin, bone, cartilage (specific tissue derived bioink), TnR Mesh (Bioresorbable scaffold)
-
Contacts:
web: tnrbiofab.com
e-mail: info@tnrbiofab.com
tel: + 82-31-431-3344
UpNano
The continuing trend towards miniaturization delivers ever more compact and powerful products. The requirements placed on microparts in the production sector, as well as academic and industrial research are constantly rising. To keep up with these developments new manufacturing standards are needed. We establish high-resolution 3D-printing as a supplement to established tooling-based fabrication methods.
UpNanos novel and innovative 3D-printing process enables economical production of polymeric microparts with highest precision and resolution in the 100 nm range, without exceeding tolerances. The lead product NanoOne combines the precision of 2-photon polymerization with unmatched throughput. And thus, economic efficiency!
Learn More about UpNano
True to the slogan ‟small, fast, powerful”
small high-resolution desktop printing system with sub-micron resolution
With 700x580x610 mm the NanoOne printing system is not only suitable for production halls but also fits in the narrowest lab, enabling economic production of polymer parts from micro to mesoscale.
fast up to a 100 times higher throughput for short production cycles
UpNanos patented printing process combines highest resolution with unmatched throughput for the first time, enabling new application possibilities and production approaches.
powerful high power laser for mesoscale and biological applications
Despite the high power the laser is gentle to cells, enabling not only the fabrication of precise and complex mesoscale structures but also bioprinting in the presence of living cells.
UpNano aims to become technology leader in the field of high-resolution 3D-printing for both prototyping and industrial applications, providing its customers with comprehensive solutions from a single source. Apart from the advanced 3D-printing system NanoOne operated via a highly intuitive and user-friendly software, the product portfolio encompasses a range of process-matching materials, from classical photopolymers, to hybrid organic-inorganic materials and hydrogels for biomedical applications.
The optimized process along with the advanced biocompatible materials, for the first time enables high-resolution 3D-printing with living cells and realization of tissue engineering scaffolds of relevant size. Thereby the cells can already be pre-mixed into the material before 3D-printing or be seeded onto a ready structure. These innovations benefit the areas of cell and tissue research and will facilitate efficiency and reproducibility of the experiments potentially revolutionizing pre-clinical research.
Wake Forest Institute for Regenerative Medicine
Our Mission: To improve patients’ lives by developing regenerative medicine therapies and support technologies.
The Wake Forest Institute for Regenerative Medicine is recognized as an international leader in translating scientific discovery into clinical therapies. Its physicians and scientists were the first in the world to engineer laboratory-grown organs that were successfully implanted into humans. Today, this team is working to engineer replacement tissues and organs and develop healing cell therapies for more than 40 different areas of the body.
Learn More about WFIRM
With the goal of speeding the process of discovery, the institute is designed for collaboration – scientists in the fields of biomedical and chemical engineering, cell and molecular biology, biochemistry, physiology, materials science, nanotechnology, genomics, proteomics, surgery and medicine work side by side. The institute has invested in a Good Manufacturing Practices/Good Tissue Practices facility which operates under guidelines of the U.S. Food and Drug Administration to hasten the delivery of technologies to patients. Several regenerative medicine therapies developed by the institute scientists are already in patients, and others in the pipeline.
Institute research focuses on a wide range of engineered replacement tissues and restorative cell therapies with the aim of making a lasting impact on conditions ranging from diabetes to heart disease. Projects range from engineered heart valves and blood vessels to technology to print skin cells directly on burns. The institute is working to apply the science of regenerative medicine to battlefield injuries through leading a $75-million federally funded project, the Armed Forces Institute for Regenerative Medicine II.
The institute offers a full range of educational and training programs to expose and educate students, teachers, scientists and the public. These programs highlight career opportunities in the biosciences while attracting the next generation of talent in the field of regenerative medicine. Programs include the annual Regenerative Medicine Essentials Course, High School Summer Research Exposure Program, Visiting International Scholars Program, Summer Scholars Program and National Institutes of Health Predoctoral Training Program.
More than 450 scientists collaborate on regenerative medicine research at the institute, the largest in the world. The institute is part of Wake Forest University and is located in the Innovation Quarter in downtown Winston-Salem, NC. Through partnerships and collaborations with many regenerative medicine centers internationally, the institute, which is driven by the urgent needs of patients, is making a global difference in the world of regenerative medicine.
336-713-7293
regenmed@wakehealth.edu
@WFIRMnews
Twitter and Facebook